Les goulots déterminent à la fois le débit et les niveaux des stocks
Considérons une chaîne de production constituée de machines non goulots (parties I et II) et d'une machine goulot.
La partie II qui se trouve derrière la machine goulot G est en sur-capacité car elle se trouve derrière la machine goulot dont la capacité est plus faible et qui limite le débit.
On peut donc considérer que cette partie est relativement stable car les aléas sont compensés par la réserve de capacité et que les temps de production prévisionnels sont relativement fiables et stables.
Aussi le stock généré en fin de chaîne va dépendre directement de la machine goulot.
En effet la date de réalisation du stock est relativement fiable car elle est donnée par celle de la machine goulot plus le temps de production de la partie II.
Si la machine goulot produit trop en avance elle va générer un stock.
Le stock moyen sera d'autant plus grand que la machine goulot produira en avance, celle-ci détermine bien le niveau des stocks.
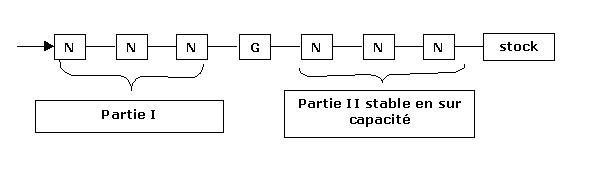
Taille des lots de fabrication
Dans la logique OPT un débit maximum des goulots est recherché (voir règle 4, une heure perdue sur un goulot est une heure perdue pour tout le système).
Les temps d'utilisation des goulots et des non goulots peuvent se présenter ainsi :
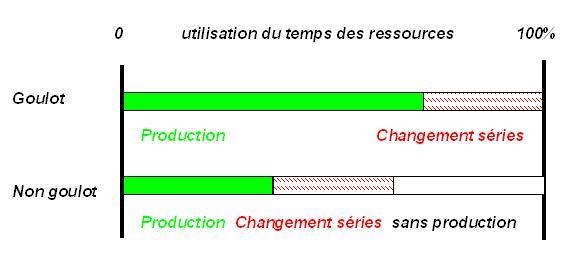
Taille des lots sur les goulots :
Les temps sont décomposés en temps de changement de série et temps de production pour les goulots.
Comme les goulots limitent le débit des pièces il faut augmenter leur temps de production et donc minimiser les pertes de débit dues aux temps de changement de série (voir méthode Smed) en les diminuant.
Par contre, contrairement à l'approche classique où la taille des lots est celle dite économique dans la méthode OPT, cette taille de lots n'est pas fixe mais elle préconise une taille variable déterminée dynamiquement en fonction de la demande.
Ce n'est plus une donnée, elle est calculée à chaque lancement. Certains processus néanmoins ne sont pas flexibles et leurs temps de série ne peuvent être rendus négligeables aussi les tailles des lots peuvent rester importantes.
Il faut alors réaliser un compromis entre les pertes de débit d'un côté et de l'autre le respect des délais et l'augmentation des encours.
Taille des lots sur les non goulots :
Les non goulots possèdent des réserves de capacité qui permettent de pallier les aléas ainsi que les déséquilibres dus par exemple à des tailles de lots trop importantes.
Il serait tentant d'utiliser cette réserve en temps de changement de série ce qui permettrait de diminuer la taille des lots de production, mais la gestion par les contraintes préconise de laisser cette réserve de capacité afin de pallier d'éventuelles surcharges ponctuelles et de consacrer ce temps perdu pour le personnel à l'amélioration continue.
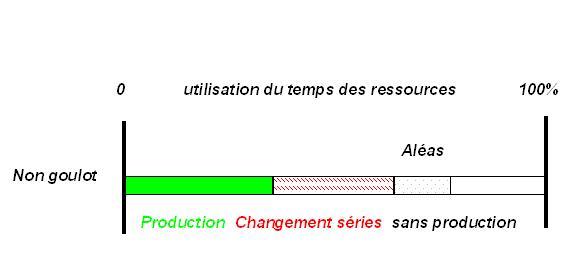
Lot de transfert et lot de fabrication
La gestion d'un atelier par les contraintes comme d'autres préconise de minimiser la taille des lots de transfert ainsi que les coûts et les délais de transfert.
La solution idéale étant un lot de transfert d'une pièce à condition que l'implantation, les systèmes de transfert soient bien adaptés (exemple l'automobile).
Définition : Lot de transfert
Quantité de pièces transférée d'une ressource à l'autre.
Définition : Lot de fabrication
Quantité de pièces produite sur une ressource entre deux changements de série.
Exemple :
une ligne de fabrication avec 4 postes (3 non goulots (N1, N2, N3 ) et un goulot G).
Dans le deuxième cas on conserve un lot de fabrication de 200 mais les lots de transfert ne sont plus que de 50 pièces, ce qui permet de gagner un temps considérable (presque 3h) sans gros investissement en réalisant simplement des actions en parallèle.

Dans le premier diagramme de Gantt les lots de transfert sont égaux aux lots de production : 200.
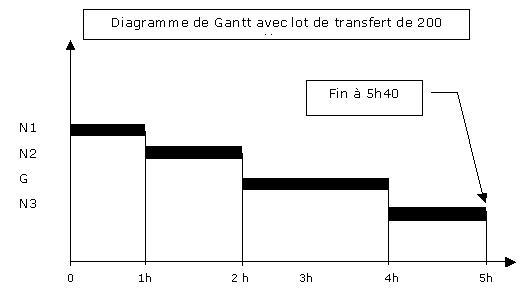
Dans le deuxième cas on conserve un lot de fabrication de 200 mais les lots de transfert ne sont plus que de 50 pièces, ce qui permet de gagner un temps considérable (presque 3h) sans gros investissement en réalisant simplement des actions en parallèle.
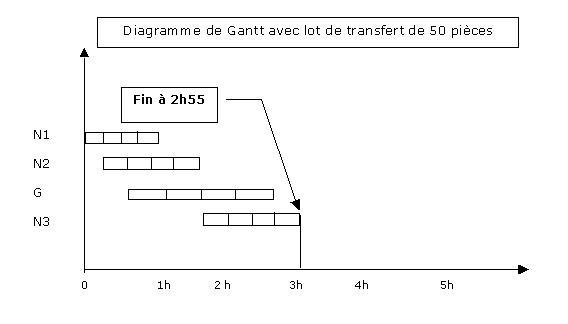
Détermination des temps de fabrication :
Pour déterminer le temps de fabrication d'un lot de pièces sur un poste de production on procède de la façon suivante :
T= ts +tu *n + D
ts : temps série est le temps nécessaire (réglages de la machine, changement d'outillages, etc.) pour changer de série ou de lot de fabrication.
tu : est le temps pour fabriquer une pièce et n le nombre de pièces du lot.
D : étant le délai moyen de transfert sur le poste suivant (y compris les temps d'attente).
Dans une logique traditionnelle MRP le temps est estimé puis inséré dans le logiciel de gestion de production.
C'est ce temps qui permettra de calculer les dates des ordres de fabrication.
Mais le temps réel de fabrication peut être complètement différent du temps estimé.
Il peut survenir des aléas aussi bien lors du changement de série (difficultés de réglages, régleur absent, pannes) que lorsque la machine produit (dérive de la machine, opérateur nouveau, arrêts intempestifs dus à des problèmes de maintenance non résolus etc..) ou pour réaliser le transfert.
Ainsi les calculs réalisés pour lancer les fabrications sont réalisés à partir de temps de fabrication inexacts.
La gestion par les contraintes préconise d'établir les programmes en prenant en compte l'ensemble des contraintes en temps réel, ainsi le temps de fabrication ne serait plus une donnée figée mais serait déterminé par le programme.