Stratégies traditionnelles face à une demande diversifiée de faible volume
Produit unique
La stratégie adoptée par Volkswagen qui ne fabriqua pendant longtemps qu'un seul modèle de voiture, la fameuse « coccinelle » n'est plus envisageable car l'offre a dépassé la demande.
Habileté
Les réglages nécessitent une certaine habileté à monter et démonter les pièces, et aussi à mesurer, centrer, ajuster et calibrer des pièces d'essai. Beaucoup d'entreprises ont essayé d'élever le niveau d'habileté de leurs ouvriers mais très peu ont essayé d'abaisser le niveau d'habileté nécessaire aux réglages.
Pour des commandes répétitives, même si chaque commande est faible, le nombre de réglages peut être réduit en rassemblant plusieurs lots en un seul.
Taille des lots
Si la taille des lots augmente, le ratio du temps de réglage par rapport au nombre d'opérations peut être fortement réduit.
Exemple :
Comme le tableau l'indique, l'accroissement de taille de 100 à 1000 pièces entraîne une réduction des heures de main-d'œuvre de 64%. Quand la taille du lot est ensuite décuplée passant à 10 000 pièces, la diminution en heures de main-d'œuvre est seulement de 17%.
En d'autres termes, l'accroissement de la taille d'un petit lot entraîne une diminution relativement importante des heures de main-d'œuvre, mais quand la taille augmente la vitesse de réduction des heures de main-d'œuvre diminue. De même, les gains entraînés par l'accroissement de la taille des lots sont plus importants pour des réglages longs que pour des réglages courts.
Ainsi si l'on suit cette logique de diminution de coût de main-d'œuvre il faudrait produire des lots très importants mais cela présente des inconvénients :
les stocks augmentent et ils coûtent cher en frais financiers, en locaux, en gestion.
Donc il existe un équilibre entre le gain de coût de main-d'œuvre grâce à la production par lots importants et la perte due à l'accroissement des stocks.
C'est la notion de série économique ou de lot économique qui est obtenue grâce à la courbe ci-dessous :
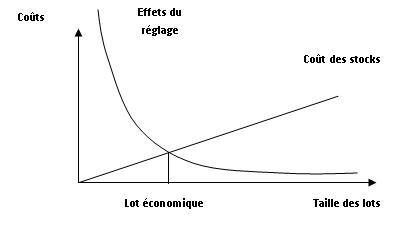
La théorie de la série économique est apparemment correcte. Mais ce concept cache une énorme faille : la supposition implicite que des réductions drastiques des temps de réglage sont impossibles.
Si un réglage de 4 heures était réduit à 3 minutes (et l'adoption du système SMED a réellement rendu cela possible) alors, même sans augmenter la taille du lot, le ratio heures de réglage - heures d'opération peut être considérablement réduit. Ceci étant, des efforts pour atténuer les effets des temps de réglage par la production de grandes séries seraient sans valeur.
En exemple, examinons les effets de l'accroissement de la taille des séries par un coefficient de 10 sur une opération dont le temps de réglage est de 3 minutes.
Dans ce cas, la réduction des heures de main-d'œuvre sera seulement de 3%. De plus, si 10 lots sont regroupés, les économies en temps de réglage en résultant seront :
3 minutes x (10 - 1) = 27 minutes
Si un jour le travail dure 8 heures, la réduction est d'à peine 0,06 % par jour. Supposons que le temps de réglage était auparavant de 4 heures. Réduire cette durée à 3 minutes aura pour conséquence une formidable augmentation à la fois de la cadence de travail et de la capacité productive.
En plus, les stocks peuvent être maintenus à un niveau minimum puisqu'il n'y aura pas d'obstacle à la production par petites séries : la question de la taille de la série ne sera même pas à l'ordre du jour. C'est pourquoi il a été dit récemment qu'avec le développement du SMED le concept de la série économique a disparu de l'arsenal de l'amélioration des coûts.
En plus, puisque le SMED peut réduire de façon significative le niveau d'habileté requis pour les réglages, le besoin d'opérateurs habiles est grandement éliminé.
La méthode SMED
Le SMED (Single-minute exchange of die)
ou changement d'outils en quelques minutes est une solution qui ne modifie pas le nombre de réglages mais s'attache à diminuer la durée du réglage.
Le réglage peut se décomposer en plusieurs étapes :
• Préparation, démontage, vérification des outillages, de la matière première,
• Montage et démontage des outils,
• Centrage, réglages des dimensions et autres paramètres,
• Pièces d'essais et d'ajustement.